Introduction
The Su-27 was designed by Sukhoi OKB as a heavy fighter for the Soviet Air Force (Voenno-Vozdushmiy Sily - VVS) and National (Homeland) Air Defense Forces (Protivo-Vozdushnoi Oborony - PVO) to regain air superiority over the F-15 Eagle operated by the US Air Force. In fact, the requirements were based on the performance of the F-15 adding ten percent. The Sukhoi design fulfilled the requirements and beyond. The Su-27 is often proclaimed the best and most successful Russian fighter of the Cold War era.
After the end of the Cold War and USSR, the Sukhoi OKB (often in cooperation with the KnAAPO plant) developed various advanced variants aimed at prospective foreign customers. The aircraft were marketed at international air shows, putting up superb aerobatic displays. The aircraft performance both on paper as in aerobatic displays has stunned many enthusiasts and experts alike all over the world. Also, the Flanker has proven its air superiority in combat during several African wars. The Su-27 and its derivatives are today some of the most popular fighters to be discussed by both aviation enthusiasts and experts.
Design
The main feature for the success of the Su-27 design is its aerodynamic configuration, known as 'integrated aerodynamic concept' by its designers. This configuration is one with extremely blended wing and fuselage. The low-aspect ratio trapezoidal midwing is fitted with large leading-edge root extensions (LERX) and blending into the fuselage creating a single lifting body.
The aircraft has a near-zero static stability and thus require a fly-by-wire system. The SDU-10 pitch-only fly-by-wire system controls the pitch of the aircraft to ensure stability and controllability for the pilot, increase aerodynamic performance, limit overload and angle of attack when needed and decrease the airframe aerodynamic load.
Two AL-31F afterburning turbofans are placed in seperate, widely spaced engine nacelles that are mounted under the lifting body. The air intakes are fitted with variable ramps.
The Su-27 has twin vertical fins fitted on the outer sides of the fuselage and twin central fins underneath. The airbrake is placed in the center of the mid-section of the aircraft behind the cockpit. The tricycle landing gear of Su-27 and Su-27UB has a single wheel on each strut. The nose wheel is fitted with a mudguard to protect against foreign object damage (FOD).
Systems & Avionics
The basic Su-27 is fitted with the SUV-27 fire control system, which incorporates the RLPK-27 radar sighting system, OEPS-27 electro-optical sighting system, SEI-31 integrated indication system, IFF interrogator and built-in test system. The fire control system in integrated with the PNK-10 flight navigation system, radio command link, IFF system, data transmission equipment and EW self-defence system.
The RLPK-27 system and is controlled by the Ts-100 digital computer and includes the N001 pulse-Doppler lookdown-capable radar with a range of 80-100 km in the front hemisphere and 30-40 km in the rear hemispehere for a fighter-sized target. It can simultaneously track up to ten aerial targets in track-while-scan mode and provide interception of the top priority target.
The OEPS-27 electro-optical sighting system consist of the OLS-27 infrared/laser search-and-track system (IRST) and the Shchel-3UM helmet-mounted target designator and is controlled by the Ts-100 digital computer. The OLS-27 sensor is placed forward of the cockpit canopy in the centre. The system acquires and tracks aerial targets by their thermal signatures. The helmet-mounted sight and the laser range finder of the IRST can also be used to visually acquire and determine coordinates of air and surface targets.
The SEI-31 integrated indication system provides flight, navigation and sighting data on the ILS-31 head-up display (HUD) and CRT. The EW self-defence systems provides warning to the crew when illuminated by enemy radar and employs both passive and active countermeasures. The aircraft is equipped with the SPO-15 Beryoza RWR and APP-50 IR decoy dispenser. Chaff dispensers are placed in the tail section between the engine nozels. In addition, the aircraft can carry the Sorbtsiya active ECM pods on its wingtips.
Cockpit
The cockpit is fitted with the K-36DM Series 2 ejection seat. The seat-back is being inclined at an angle of 17 degrees. In the two-seat Su-27UB version, the seats are placed in tandem with the rear-seat being elevated to ensure good forward vision. The basic Su-27 cockpit layout consist of analogue instruments, HUD and CRT display to display data from radar and electro-optical sight (IRST). On both sides of the HUD control panel, there are sensors for the helmet-mounted target designator system. On the right side below the CRT display the RWR indicator is placed.
Weapons
The Su-27 is fitted with one GSh-301 automatic single-barrel 30mm cannon fitted inside the starboard wing LERX. It can be armed with up to 150 high explosive incendiary or armour piercing tracer rounds.
The basic Su-27's primary armament consists up to six R-27R/ER semi-active radar homer or R-27T/ET heatseeking homer medium range air-to-air missiles, as well as four R-73 IR agile all-aspect short range air-to-air missile. The basic Su-27 has only a limited air-to-surface capability consisting of only unguided bombs and rockets.
Upgrading the Russian Air Force Su-27 fleet
The Russian Air Force received its first batch of upgraded Su-27s in 2006. The air force seems to have settled for the mid-life upgrade offered by KnAAPO based on the Su-30MK2, which brings the aircraft up to Su-27SM standard. The Su-27SM is equipped with an upgraded fire control system including the improved N001V radar with phased array antenna, which offers improved performance and air-to-surface mode. The new system enables the use of the RVV-AE (R-77) medium range air-to-air missile and a wide selection of guided air-to-surface bombs and missiles. Another heavily updated feature is the cockpit, which is upgraded with three MFD, new HUD, satellite receiver and new communications set. The aircraft's self-defense suite has also been upgraded.
The Russian Air Force plans to upgrade its entire fleet to Su-27SM standard, but the exact number of aircraft involved remains unclear.
The Su-27SM is based on earlier proposed upgrades for the Su-27SK export version. The Su-27SMK as it is designated has seen two attempts, with at the basis a different radar system (N001M and N001VEP respectively). China was seen as the premier customer for an upgrade package. However China opted to expand its Flanker fleet with multi-role Su-30MKK and Su-30MKK2 instead of upgrading its Su-27SK and J-11 single-seaters. Instead China planned an indigenous upgrade for its J-11s. Other clients also preferred two-seat Su-30MK/MK2. From 2002 onwards, Sukhoi and KnAAPO developed a new deeply modernized single-seat Su-27 derivative known as Su-27BM. Designated Su-35, it will be offered for new export orders, replacing the previously offered Su-35, which was based on the Su-27 and offered in the 1990s.
Based on the Su-35(Su-27BM), the Su-27SM2 upgrade is on offer to the Russian Air Force for the second phase of its Su-27 mid-life upgrade program. The Su-27SM2 upgrade will give Russia's existing Su-27s a similar avionics and weapons suite as offered on the Su-35(Su-27BM). The Russian Air Force has expressed interest in the Su-35, but it remains to be seen whether this will include new air frames or be limited to the Su-27SM2 upgrade.
Upgraded Su-27 Flankers for the Russian Air Force are also planned to be fitted with upgraded engines. Both MMPP Salyut and NPO Saturn have developed modernized and more powerful AL-31F variants. In December 2006, the MMPP Salyut's AL-31F-M1 turbofan passed state acceptance tests for use on the Su-27SM. The AL-31F-M1 produces 132.4 kN (29,765 lb) of thrust in an additional mode, 9.8 kN (2,203 lb) more than the standard AL-31F turbofan. It will be followed by the AL-31F-M2 and the even more powerful AL-31F-M3 with 147.1 kN (33,069 lb) of thrust is also under development to compete for the first stage of the PAK-FA program, Russia's future fifth generation fighter. Rival NPO Saturn meanwhile developed the izdelye 117S, another AL-31F derivative based on the AL-41F which produces 142.2 kN maximum thrust. Co-funded by Sukhoi and UMPO, the 117S will enter series production both at Saturn and UMPO to power the Su-35 export fighters. On Febuary 19, 2008, the firstSu-35 prototype made its maiden flight powered by two 117S. NPO Saturn is also competing to power the PAK-FA with a further modified 117S. Pending a decision on the powerplant selection for the 'first stage' of the PAK-FA program, it remains to be seen which of the options will power the Su-27SM/SM2 upgrades.
The two-seat aircraft will most likely be upgraded to Su-27UBM. Although IAPO offered such an upgrade demonstrated on the Su-30KN, it remains unclear whether the Russian Air Force has opted for this upgrade or plans to have KnAAPO update the two-seaters under a similar program as the Su-27SM/SM2.
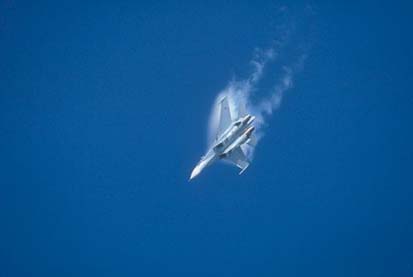
Primary Function: | Air superiority fighter |
Contractor: | Sukhoi |
Crew: | One |
Unit Cost: | N/A |
Powerplant | |
Two NPO Saturn AL-31F turbofans each rated at 17,857 lb (79.43 kN) dry thrust and 27,557 lb st (122.58 kN) with afterburning | |
Dimensions | |
Length: | 71 ft, 11.5 in (21.935 m) |
Wingspan: | 48 ft, 2.75 in (14.7 m) |
Height: | 19 ft, 5.5 in (5.932 m) |
Weights | |
Empty: | 39,021 lb (17700 kg) |
Maximum Takeoff: | 66,138 lb (30000 kg) -- Flanker-B |
Performance | |
Speed: | Mach 2.35 (1,553 mph; 2500 km/h) |
Ceiling: | 59,055ft (18,000m) |
Range: | N/A |
Rate of Turn: | 22.5° / sec Sustained 28.5° / sec Instant |
Su-27 Flanker Family Armament
Aircraft with 10 hardpoints (Su-27, Su-27UB, Su-27SK, Su-27UBK, Su-30KI)
8 | 6 | 4 | 10 | 1,2 | 9 | 3 | 5 | 7 | |||
Internal: GSh-301 (150 rounds) | |||||||||||
Guided A-A: R-73 R-27ER R-27ET RVV-AE | 1X | 1X | 1X 1X 1X 1X | 1X 1X | 2X 2X | 1X 1X | 1X 1X 1X 1X | 1X | 1X | ||
Unguided A-S: FAB-500M62/RBK-500/ZB-500 FAB-250M54 FAB-250M62 OFAB-100-120 B-8MI B-13L S-25 | 1X 1X | 2X 6X 3X 6X 2X 2X 2X | 1X 5X 2X 6X | 2X 7X 6X 12X | 1X 5X 2X 6X | 1X 6X 3X 6X 2X 2X 2X | 1X 1X | ||||
Guided A-S: Kh-29T * Kh-31P(A)* Kh-59M* KAB-500Kr * KAB-1500Kr * | 1X 1X 1X 1X 1X | 1X 1X 1X | 2X 1X | 1X 1X Tekon 1X | 1X 1X 1X 1X 1X | ||||||
* guided air-to-surface weapons can only be used with upgraded fire control system ** stations 1 and 2 are placed in tandem between engine nacelles | |||||||||||
Source: Fomin, A., Su-27 Flanker Story Copyright © 2008 Niels Hillebrand - MILAVIA.NET | |||||||||||
Aircraft with 12 hardpoints (Su-35, Su-30MK, Su-33*)
8 | 6 | 4 | 12 | 10 | 1,2 | 9 | 11 | 3 | 5 | 7 | |
Internal: GSh-301 (150 rounds) | |||||||||||
Guided A-A: R-73 R-27ER R-27ET RVV-AE | 1X | 1X | 1X 1X 1X 1X | 1X 1X | 1X 1X | 2X 2X | 1X 1X | 1X 1X | 1X 1X 1X 1X | 1X | 1X |
Unguided A-S: FAB-500M62/RBK-500/ZB-500 FAB-250M54 FAB-250M62 OFAB-100-120 B-8MI B-13L S-25 | 1X 1X | 2X 6X 3X 6X 2X 2X 2X | 1X 5X 6X | 1X 5X 2X 6X | 2X 7X 6X 12X | 1X 5X 2X 6X | 1X 5X 6X | 1X 6X 3X 6X 2X 2X 2X | 1X 1X | ||
Guided A-S: Kh-29T * Kh-31P(A)* Kh-59M* KAB-500Kr * KAB-1500Kr * | 1X 1X 1X 1X 1X | 1X 1X | 1X 1X 1X | 2X 1X | 1X 1X Tekon 1X | 1X 1X | 1X 1X 1X 1X 1X | ||||
* guided air-to-surface weapons can be used by Su-33 fighter only with the upgraded fire control system ** stations 1 and 2 are placed in tandem between engine nacelles | |||||||||||
Source: Fomin, A., Su-27 Flanker Story Copyright © 2008 Niels Hillebrand - MILAVIA.NET |